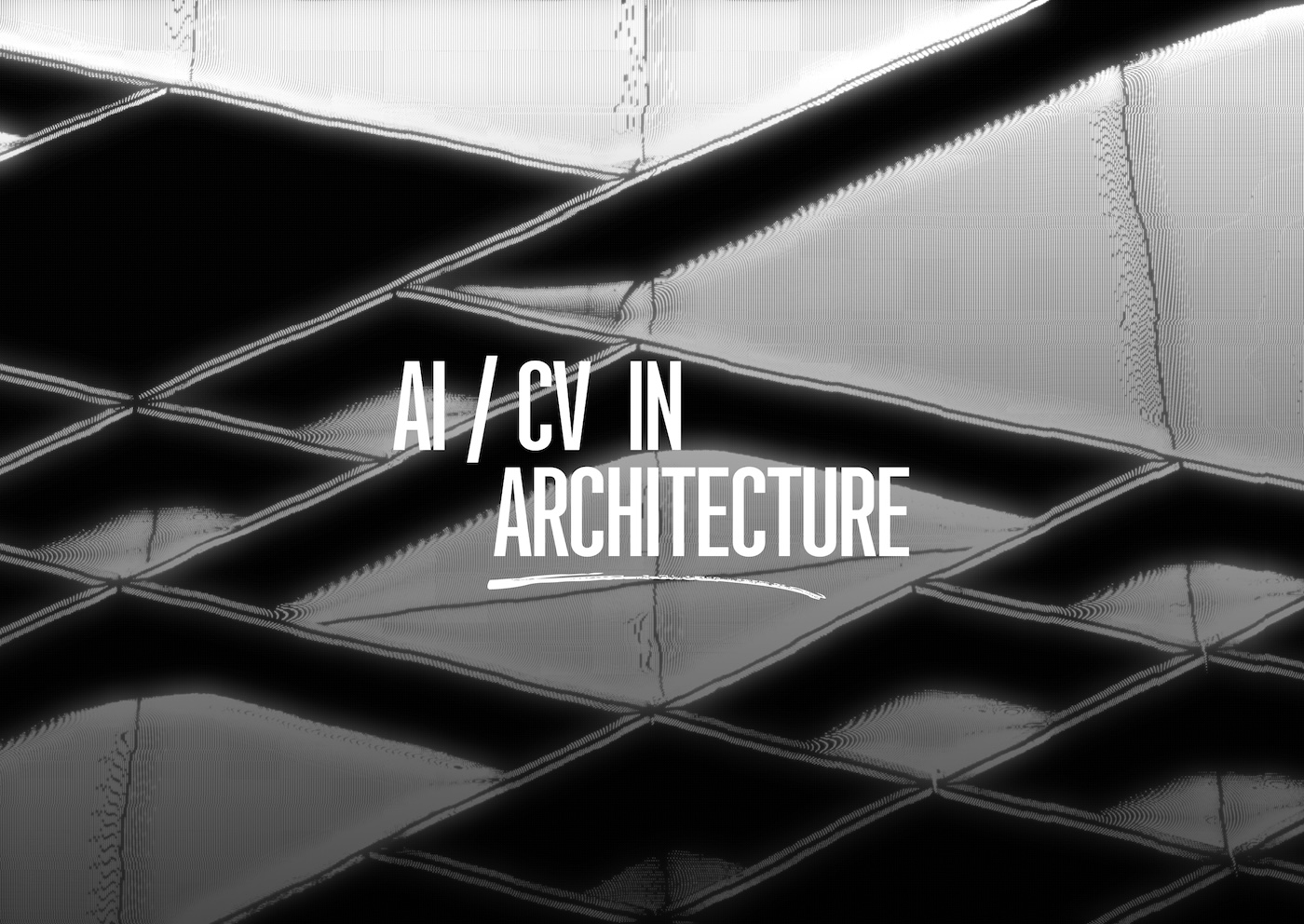
Artificial intelligence and computer vision today is one of the key drivers of manufacturing in general. For example, the introduction of AI in Ford's assembly plants has allowed the company to speed up car assembly by 15% without upgrading the production facilities — AI was able to find bottlenecks and speed up what seemed to be extremely fast already.
Not surprisingly, according to a Deloitte survey, 58% of companies plan to implement computer vision in manufacruring in their operations in the coming years.
The first digitalization technologies have been used in the industry since mid-1960s — when still imperfect computers and programs were used to convert two-dimensional drawings into three-dimensional ones.
Here are some examples of technologies that are being used in manufacturing right now!
Google has introduced a Visual Inspection AI technology specifically for manufacturing. The AI in manufacturing is claimed to provide 10 times better inspection of chips and other electronic components. At the same time, 300 times fewer human-marked images is enough to train the model than for similar general solutions.
At the same time, there are solutions that allow you to check the assembly quality of large equipment. For example, Hepta Airborn helps to identify defects in the assembly of high-voltage wires, in which case the equipment is inspected automatically by drones.
General Electric uses computer vision technology to monitor turbine production. The company is actively trying on 3D printing, including highly loaded components that operate at high temperatures. 3D printing has made it possible to reduce the number of parts in a turbine from 800 to a few dozen.
And computer vision solutions for manufacturing helps to print everything accurately and without defects: the AI monitors the process continuously, stopping printing if a defect occurs. This has helped to get rid of expensive, long, and complicated defectoscopy after assembly.
A prime example of fully automated manufacturing is Tesla. The widespread usage of AI and computer vision technology for manufacturing has enabled the company to reduce the assembly time of electric vehicles by 50% or more. And plans to create a modern electric car costing less than 25 thousand dollars are not feasible without such production facilities. AI and CV allows us to squeeze the most out of any, even the most advanced production.
Of course, computer vision technology is not only used to speed up production, but also to keep people safe. We tell you more about it in our other article.
For example, parallel assembly of components that previously required separate workshops has allowed Tesla to reduce the size of its Gigafactories by 10%. The company has even learned to simultaneously install both batteries under the floor and interior components with seats.
To create the frames of its cars, Tesla created a super press with an exert-a-force of more than 6,000 tons. As a result, the frame consists of just 3 forgings — each of which is carefully inspected after production using computer vision and fluoroscopy.
Artificial Intelligence helps not only in manufacturing but also in designing new things too. Such a computer vision system for manufacturing is used in Ford, where new car models are created using augmented reality technology from Microsoft eyewear. This greatly speeds up the machine development process, and allows dozens of engineers to work on a single 3D model at once. Similar solutions are used in Audi and Honda.
And AI also helps in creating complex parts and devices that are difficult to design manually. For example, using AI to place transistors on a chip in the most optimal order — or workstations and machines in a production facility. Such generative AI in manufacturing will have an increasing impact on engineering.
Robots have long been able to produce clothes more efficiently than humans (and they can save humans from one of the most tedious jobs in real sweatshops).
Tianyuan Garments aims for a fully operational production process, creating one T-shirt every 22 seconds, with plans to manufacture 800,000 T-shirts daily while cutting operational costs by 33% per T-shirt. The price to produce each shirt, including labor and materials will be approximately $0.33, significantly cheaper than what is currently possible with even the most exploitative of developing-world labor.